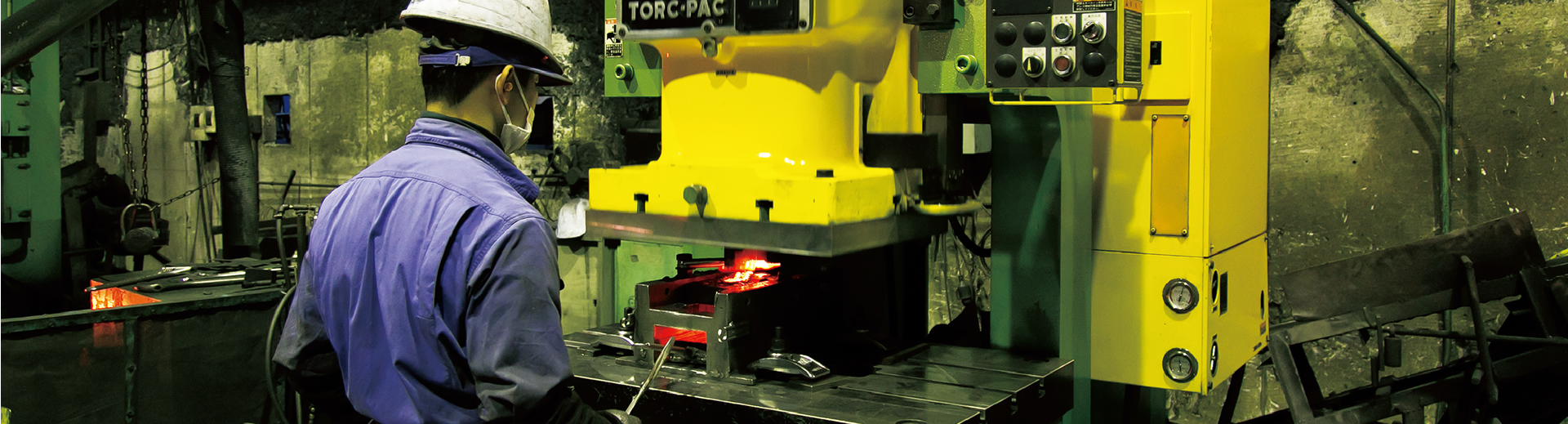
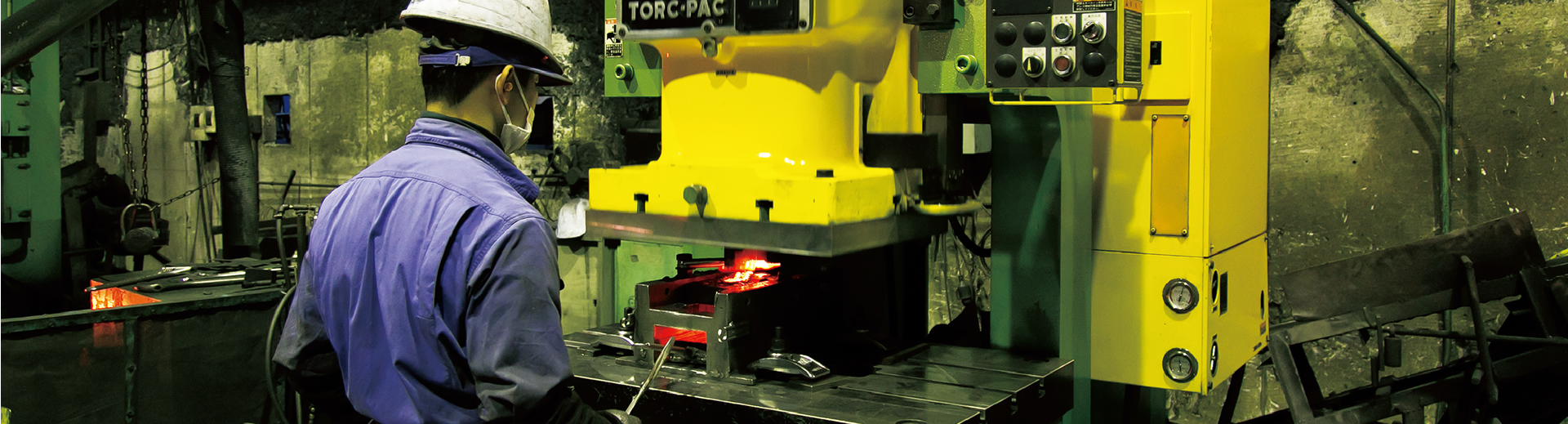
At Yamaco, each of our employees takes technology seriously
and works together with others in friendly
competition each day as they engage in manufacturing.
What we cannot do alone, we can do by working together.
This kind of strong teamwork produces excellent technology.
Episode 1
Teamwork like a relay
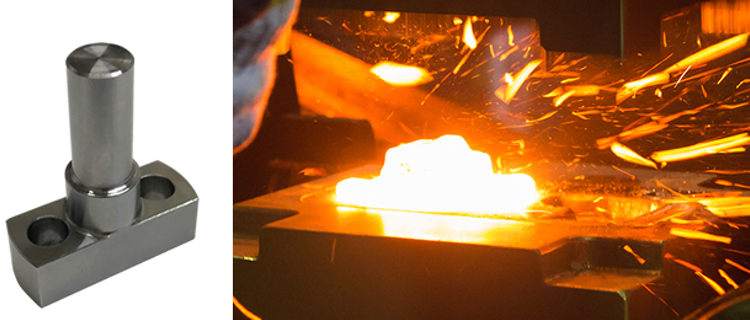
We received a request from a customer to manufacture machine parts.It was a project that included the processes from design to die manufacturing,
hot forging, machining, and inspection and normally takes a few months, but the customer would only place the order if we could deliver the products in one month.
Each of the relevant departments held discussions to work out the processes, and believing that we could shorten the period to 30 days, we received the order immediately.
Each department worked as a team to shorten the delivery time little by little by speeding up their processes and pass on the baton like a relay of athletes, and incredibly,
we completed the project in three weeks. The customer was very pleased.
This experience in which all of us worked in real earnest with one mind “for the customer” led to self-confidence
and growth in each individual, and this has become a great asset for us.
Episode 2
“Finding personal fulfillment”
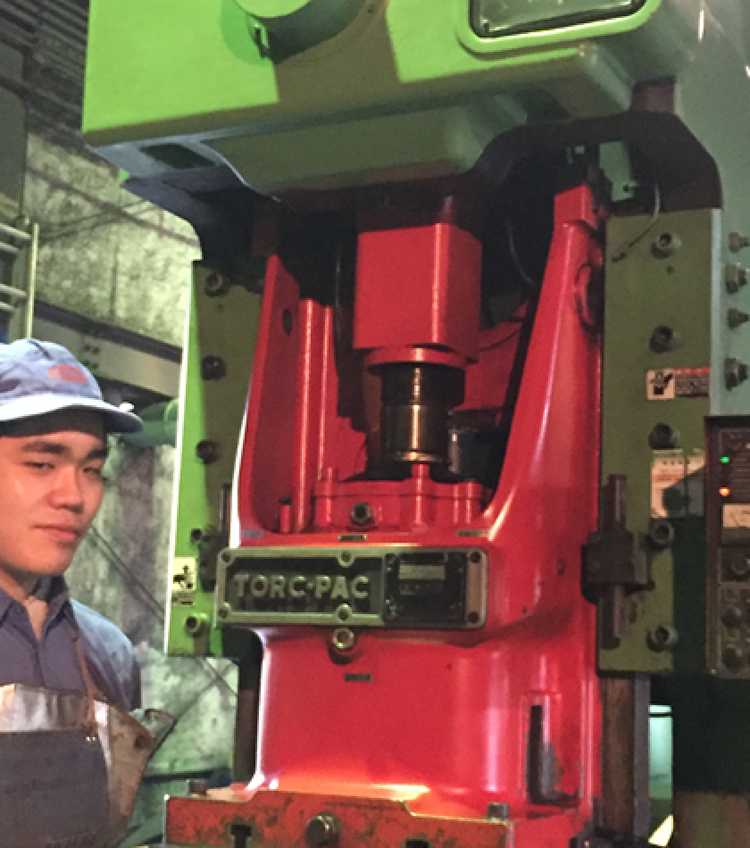
We had a machine used by several groups of employees that had parts that were never wiped even when the machine was cleaned.
Everyone thought they were spots that did not need to be wiped.At some point, a young employee began to wipe those parts. Seeing the machine get cleaner and shinier the more it was wiped, the employees in other groups also started to wipe those parts. Before anyone knew it, a “wiping to polishing” competition had begun. No matter how much they wiped, no one could beat that one young employee, and they all shouted, “He’s the winner!” When asked about it later, he said that he felt like the machine had gotten easier to use and that his daily press work had gotten better since he had felt this way. This kind of attitude leads to 3S activities, as well as to self-confidence and personal fulfillment for each employee.
The charm of Yamaco is that you are always appreciated for even the smallest things you do and there are places for everyone to flourish.
Episode 3
“YPM Kaizen activities”
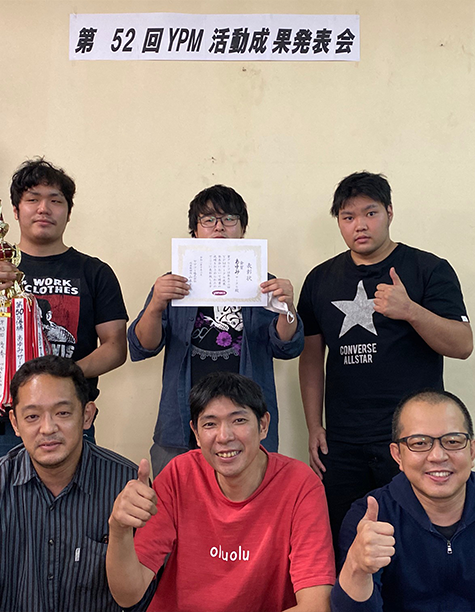
Kaizen has been introduced in the automobile and other industries where high quality and safety are required.
Yamaco refers to kaizen as “YPM Kaizen activities” and holds presentations twice a year, with this year being the 22nd year since we started.
For the presentations, each department focuses on a theme and reports on the progress of YMP once a month. On the other hand, areas for improvements are identified and thoroughly reframed at quality meetings until rules are established to improve quality, such as if operation-related problems occur, while prioritizing countermeasures and prevention.